Ключевые слова: защитное покрытие, внешний керамический слой, электронно-лучевое осаждение, микроструктура, дифрактограмма, фазовый состав.
Keywords: protective coating, outer ceramic layer, electron-beam deposition, microstructure, X-ray pattern, phase composition.
Изучено влияние технологических параметров электронно-лучевого осаждения двухслойных покрытий металл—керамика за один технологический цикл на структуру и фазовый состав внешнего керамического слоя на основе диоксида циркония, стабилизированного оксидом иттрия. Показана возможность получения покрытий металл—керамика с необходимыми функциональными характеристиками за один технологический цикл.
The influence of technological parameters of an electron-beam deposition of two-layer metal—ceramics coatings in one technological cycle on the structure and phase composition of an outer ceramic layer on the basis of zirconium dioxide stabilized by yttrium oxide is studied. The coating obtained is uniform all over the specimen surface. The width of the outer layer is shown to be affected by sample roughness.
Двухслойные защитные покрытия металл—керамика нашли широкое применение в двигателестроении для защиты лопаток газовых турбин [1—3]. Известно [1], что для осаждения внутреннего металлического слоя чаще всего используют сплавы MCrAlY (где М — никель, кобальт, железо), для внешнего керамического слоя — диоксид циркония ZrCb, стабилизированный оксидом иттрия Y2O3 (Yttrium Stabilized Zirconium Oxide, YSZ). Долговечность лопаток с подобными двухслойными покрытиями в значительной степени определяется технологичными параметрами их осаждения. Несмотря на обширные результаты исследований, посвященных данному вопросу [1—7], в литературе нет однозначных технологических рекомендаций по осаждению указанных покрытий.
Обычно для формирования двухслойных покрытий металл—керамика на лопатках турбин используют двухстадийную технологию. Внутренний металлический слой наносят на изделия с помощью вакуумного плазменного распыления (Vacuum Plasma Spray, VPS); воздушного плазменного распыления (Air Plasma Spray, APS) или электронно-лучевого физического испарения и конденсации (Electron-Вearn Physical Vapor Deposition, EB-PVD). Одним из приемов, используемых в технологическом цикле осаждения двухслойных покрытий, является дробеструйная обработка поверхности металлического слоя с последующим отжигом в вакуумной печи с целью “залечивания” дефектов структуры в осажденном слое [3]. Иногда для получения требуемой шероховатости перед осаждением внешнего керамического слоя поверхность внутреннего металлического слоя подвергают гидроабразивной обработке водной эмульсией глины [4] и только затем наносят внешний керамический слой одним из упомянутых методов.
До последнего времени в экономически развитых европейских странах и США предпочтительным методом нанесения защитных покрытий металл—керамика оставалось плазменное напыление. В некоторых ведущих двигателестроительных фирмах мира, в частности “Pratt and Whitney”, используют комбинированный метод получения двухслойных покрытий. Внутренний слой MCrAlY наносят плазменным напылением, а внешний керамический слой — электрон-но-лучевым осаждением. Использование различного оборудования, в конечном итоге, усложняет и удорожает технологический процесс осаждения защитных покрытий. Принципиальное решение задачи — нанесение двухслойных покрытий металл—керамика на одном типе оборудования и за один технологический цикл. Отметим, что эффект от применения двухслойных покрытий металл—керамика в значительной степени зависит от совершенства технологических процессов. Считается [1—3, 8], что электронно-лучевой метод осаждения внешнего керамического слоя по сравнению с плазменным нанесением имеет определенные преимущества — повышенную циклическую долговечность полученного керамического слоя при теплосменах.
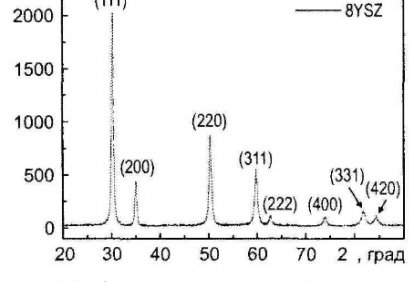
Рис. 1. Дифрактограмма исходной керамики Zr02—Y203
Цель данной работы — исследовать влияние температуры нагрева, скорости осаждения, скорости вращения, кривизны и шероховатости поверхности образцов на структуру и фазовый состав внешнего керамического слоя.
Исходные материалы и образцы для нанесения покрытий
Для нанесения внутреннего металлического слоя использовали слитки Ni—(18—22)% Сг—(6—8)% А1—(0,5—1)% Y диаметром 68,5 мм и высотой 400 мм, полученные с помощью электронно-лучевого переплава. Для осаждения внешнего керамического слоя применяли штабики керамики ZrOi—7,2 ± 0,5% Y203 (7YSZ) диаметром 68,5 мм и высотой 65 мм, полученные холодным прессованием с последующим спеканием на воздухе. Плотность штабиков после спекания составляла 3,9—4 г/см3. Спеченная керамика состояла преимущественно из стабилизированной кубической составляющей с незначительной долей тетрагональной фазы (рис. 1).
Для нанесения двухслойных покрытий металл—керамика использовали специальные образцы из жаропрочного сплава “Inconel 718”, имеющие плоскую (F) и радиальную (R) поверхности (рис. 2).
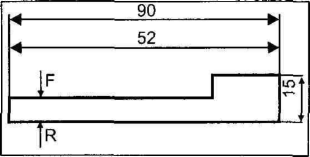
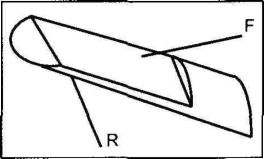
Рис. 2. Образцы для исследований
Методика нанесения двухслойных покрытий металл—керамика
Двухслойные покрытия на образцах получали с помощью лабораторной электронно-лучевой двухкамерной установки L-2 производства НПП “ЭЛТЕХМАШ” (Винница, Украина). Наличие трехтигельного испарительного устройства в рабочей камере и вспомогательной (перезагрузочной) камеры позволяет хгаждать разнообразные покрытия на изделия, параметры технологического процесса получения которых фиксируются автоматической системой. Технологическая схема получения двухслойных покрытий металл—керамика за один технологический цикл показана на рис. 3.
Образцы, предварительно обезжиренные спиртом, помещали в специальную кассету. В каждом эксперименте покрытия наносили на четыре образца. Кассету с образцами закрепляли на горизонтальном штоке во вспомогательной перезагрузочной) камере, а затем, после достижения требуемой глубины вакуума, перемещали в рабочую камеру. Скорость вращения кассеты с образцами составляла 8, 14 и 20 об-мин_|. Расстояние от оси вращения до плоскости испарения — 320 мм. Образцы 1 предварительно нагревали до температуры 950 ± 10 °С и из испарителя 3 наносили металлический (связующий) слой толщиной 50—60 мкм. Затем без разгерметизации рабочей камеры из испарителя 2 осаждали керамический слой. Температура осаждения керамического слоя составляла 750, 800, 850, 900 и 950 (±10) °С, толщина слоя 15—30 мкм.
Методы исследований
Микроструктуру керамического слоя в исходных образцах (без предварительного отжига) исследовали на сканирующем электронном микроскопе “Philips”, съемку рентгенограмм осуществляли на дифрактометре “Rigaku” с использованием монохроматического СиКа-излучения.
Экспериментальные результаты
Температура нагрева изделий при осаждении керамического слоя является одним из наиболее значимых технологических параметров процесса нанесения покрытий, определяющих структуру внешнего керамического слоя. Поскольку жаропрочные сплавы имеют ограничения по максимальной рабочей температуре, связанные с их структурной нестабильностью, то обычно покрытия на изделия из них наносят при температурах, не превышающих рабочие.
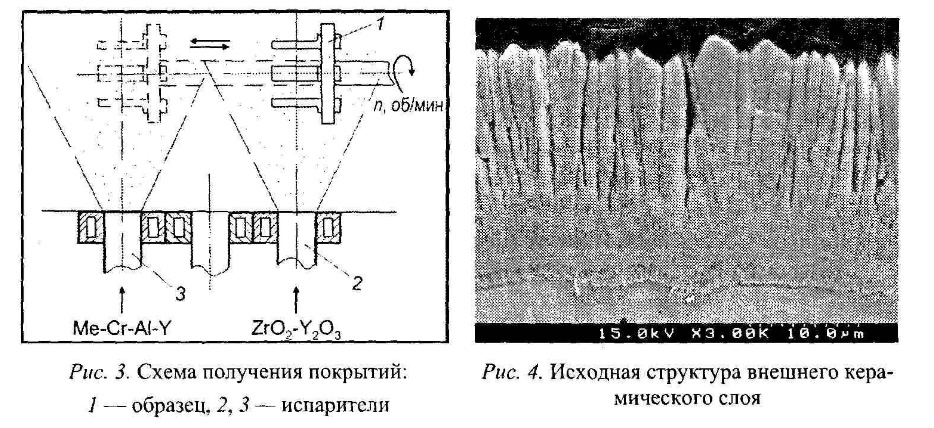
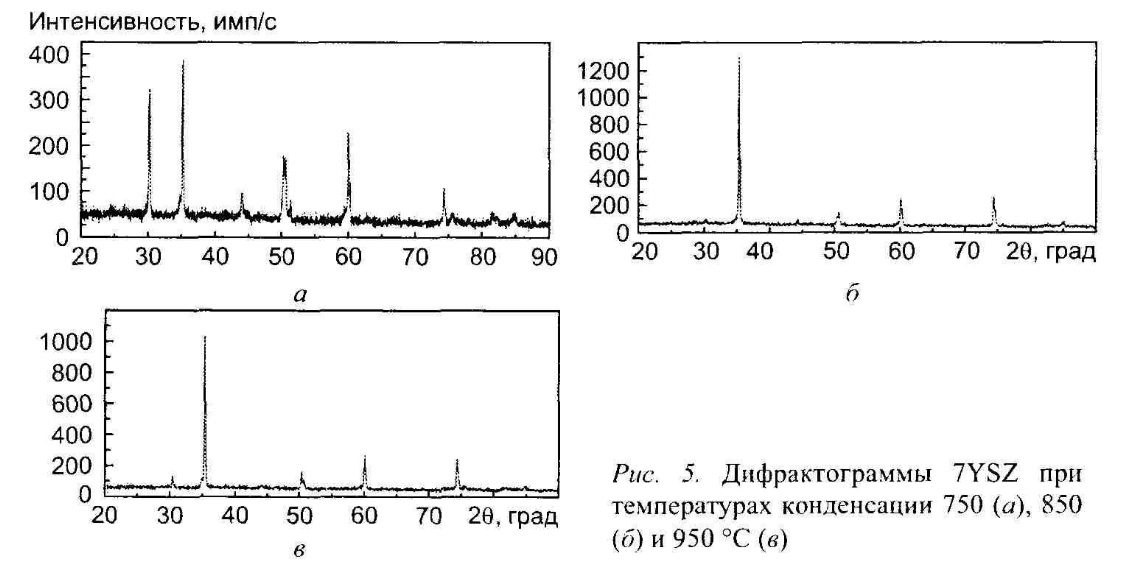
При этом в сплавах за время нагрева изделий не происходит существенных структурных изменений, а значит, не изменяются характеристики прочности и пластичности. В то же время для формирования бездефектной структуры в керамических материалах температура образцов должна быть не ниже 0,3 Гпл конденсируемого вещества [1]. Исходная структура внешнего керамического слоя защитного двухслойного покрытия, полученного при температуре конденсации 900 °С, показана на рис. 4.
Электронно-лучевые керамические покрытия отличаются существенной микроструктурной и кристаллографической анизотропией, поскольку их рост обычно происходит по различным кристаллографическим направлениям. При этом образуются каналы роста, и в итоге наблюдается значительная неоднородность плотности с минимумом у границы раздела с внешней средой и максимумом у границы раздела с защищаемым материалом. Во всех случаях при различной температуре конденсации внешнего керамического слоя керамическое покрытие имеет явно выраженную двухзонную структуру. Первая зона, высокоплотная, образуется в начале осаждения внешнего керамического слоя на границе контакта металл—керамика. В ней отсутствуют каналы роста, характерные для второй зоны. Вторая зона керамического слоя имеет рассеянную микропористость, микротрещины и сегментацию. Микротрещины, как правило, свидетельствуют о беспорядочных внутренних разрывах в керамическом слое, тогда как сегментация указывает на то, что керамический слой имеет столбчатую структуру, ориентированную перпендикулярно к поверхности образцов, причем между зернами присутствуют микротрещины.
Увеличение температуры конденсации от 750 до 950 °С вызывает рост поперечного сечения столбчатых кристаллитов керамического слоя с 0,3— 0,5 мкм до 1,0—1,2 мкм и их более полное срастание в результате выделения скрытой теплоты конденсации, увеличивающей объёмную диффузию, что приводит к снижению пористости. В керамических покрытиях, полученных при температуре конденсации до 750 °С, присутствуют поры, расположенные в основном на границе раздела металл—керамика. Их появление связано с возникающими в керамическом слое микроканалами на границах раздела кристаллитов, по которым более свободно проникают агрессивные элементы из окружающей среды к металлическому подслою.
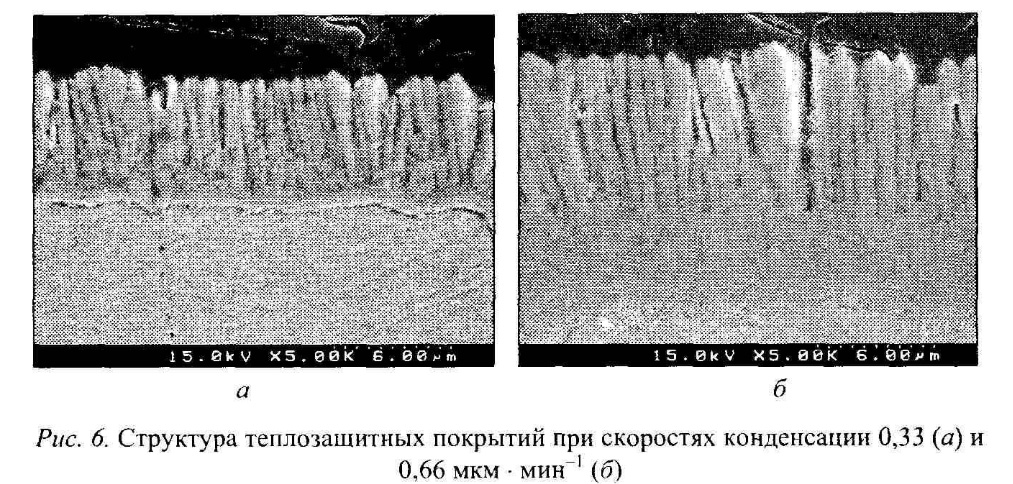
Рентгенографические исследования показали, что при повышении температуры конденсации внешнего керамического слоя с 750 до 850 °С уменьшаются внутренние напряжения и текстура роста. При низкой температуре осаждения 7YSZ этот слой имеет преимущественно высокотемпературную стабилизированную кубическую модификацию (типа флюорита). При дальнейшем увеличении температуры осаждения до 900 °С он состоит уже из двух фазовых структурных составляющих: кубической и тетрагональной, причем количество тетрагональной фазы с повышением температуры увеличивается (рис. 5).
Так как объем элементарной ячейки тетрагональной модификации на 9,5% больше, чем кубической [5], то внешний керамический слой, получаемый при температуре осаждения 900—950 °С, имеет меньшую микропористость и большую толщину (3—4 мкм) высокоплотной зоны по сравнению с аналогичными слоями, полученными при температурах осаждения 750—850 °С, где толщина этой зоны не превышает 2—2,5 мкм.
Скорость осаждения керамического слоя есть важнейший технологический параметр, определяющий структуру и свойства внешнего керамического слоя. Высокоплотная зона в керамическом слое является эффективным барьером на пути проникновения окислительной среды к поверхности металлического подслоя. При постоянной скорости вращения образцов в паровом потоке керамики увеличение скорости конденсации приводит к локальному изменению температуры на поверхности металлического подслоя и, как результат, к изменению условий образования центров кристаллизации и последующего роста кристаллитов керамики. Так, увеличение скорости осаждения с 0,33 до 0.66 мкм • мин-1 при одинаковой температуре (800 °С) приводит к росту тол-шины высокоплотной зоны 7YSZ, образующейся на границе контакта металл—керамика в начале осаждения внешнего керамического слоя, с 1,3 до 5.0 мкм (рис. 6).
Изменяя технологические режимы испарения керамики в начальный момент формирования керамического слоя на металлическом подслое, можно регулировать толщину указанной высокоплотной зоны внешнего керамического слоя. Так, при форсированном осаждении керамики (0,9—1,2 мкм • мин-1) открытием заслонки, которая экранирует образцы от парового потока при выходе на рабочий режим испарения, можно достичь толщины высокоплотной зоны до 8—10 мкм. Плавный, в течение 8—10 с, выход на режим испарения керамики при открытой заслонке позволяет получать толщину высокоплотной зоны 3—5 мкм.
Согласно литературным данным, влияние скорости вращения образцов относительно парового потока при формировании теплозащитных покрытий
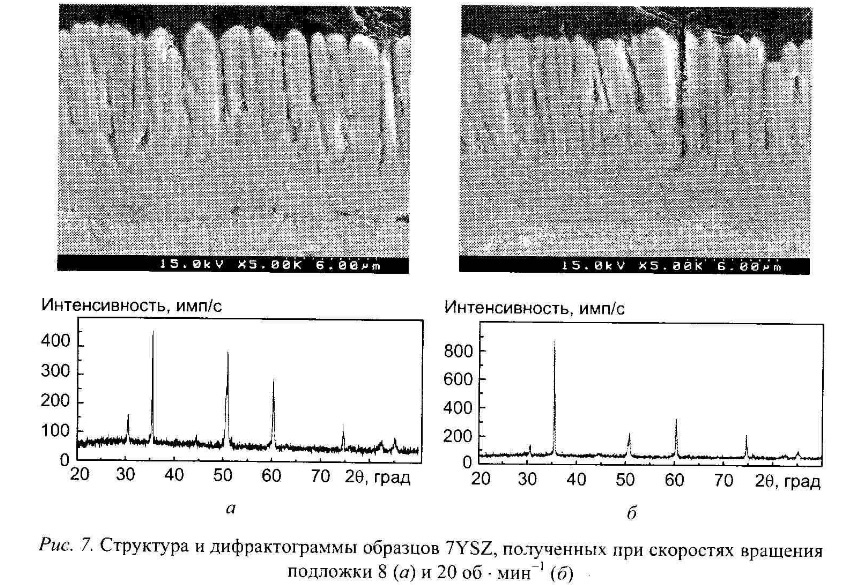
недостаточно освещен в литературе. При получении внешнего керамического слоя скорость вращения образцов изменяли от 0,5—0,6 об • мин"1 [6] до 10 об • мин-1 [5—7], однако во многих работах ее значение вообще не указано. На основании исследования структуры и дифрактограмм керамических покрытий (рис. 7), полученных при различных скоростях вращения образцов, можно сделать вывод, что при постоянной скорости осаждения керамического слоя увеличение скорости вращения образцов в паровом потоке от 8 до 20 об • мин-1 приводит к росту толщины высокоплотной зоны керамики на границе раздела металлический подслой—керамическое покрытие в 1,3 раза.
Анализ дифрактограмм керамического слоя позволил сделать вывод о том, что повышение угловой скорости вращения образцов также приводит к некоторому увеличению количества тетрагональной фазы и сохранению преимущественной ориентации роста кристаллитов(низкомодульная структура).
Профиль поверхности образцов. Типичная микроструктура керамического слоя на радиальной и плоской поверхностях образцов показана на рис. 8. Покрытие практически равноценно по всей поверхности образцов. Можно лишь отметить, что керамическое конденсационное покрытие несколько различается своей плотностью на плоскости (здесь оно более плотное) и на радиусе (более пористое), что связано с кристаллографическими особенностями роста столбчатых зерен керамики на плоской и выпуклой поверхностях профиля образцов.
Шероховатость поверхности образцов. Результаты исследования шероховатости поверхности образцов показали, что внешний керамический слой 7YSZ, нанесенный на полированную (параметр шероховатости поверхности Ra~ 0,15—0,20 мкм) поверхность, имел наиболее низкую термостойкость.
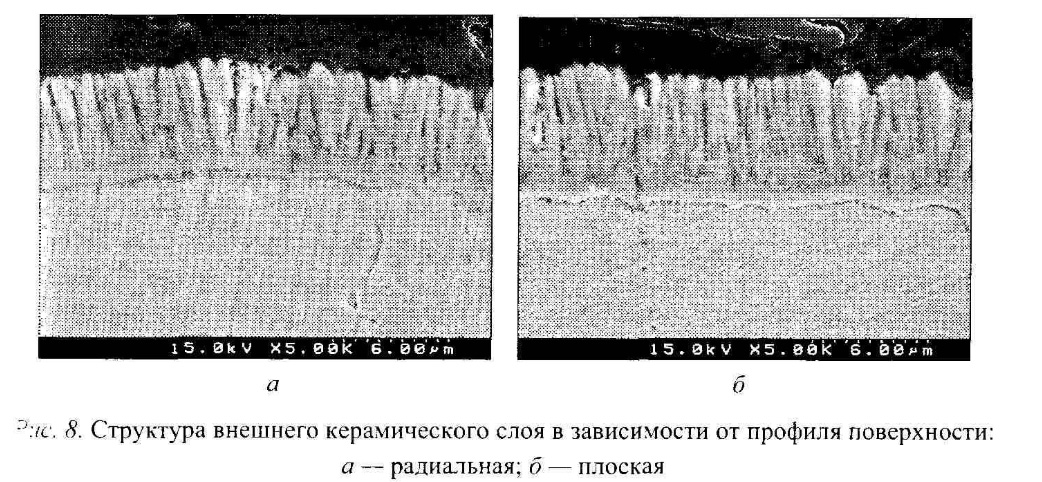
После обработки металлического подслоя микрошариками (Ra=0,7-0,8 мкм) термостойкость керамического слоя повышалась. В тоже время, как отмечалось в работе [7], уровень циклической прочности в большей мере определяется состоянием поверхности и условиями зарождения усталостных трещин. Поверхность внешнего керамического слоя с параметром шероховатости 0,6-0,8 мкм более восприимчива к зарождению усталостных микротрещин из-за наличия поверхностных концентраторов напряжений. Тем не менее циклическая прочность двухслойных образцов металл-керамика находилась на уровне циклической прочности основного металла [7]. На рис.9 показаны дифрактограммы исследованных образцов с различной исходной шероховатостью.
Анализ дифрактограмм показал, что шероховатость поверхности осаждения не влияет на фазовый состав внешнего керамического слоя и при температуре осаждения 900оС он состоит из кубической и тетрагональной составляющих. Однако при этом отмечено увеличение текстуры керамического слоя при уменьшении параметра шероховатости.
Также отметим, что уменьшение шероховатости приводит к увеличению ширины высокоплотной зоны внешнего керамического слоя от 2-2,5 мкм при Ra=6,3 мкм до 3,5-5 мкм при Ra=1,6 мкм и той же температуре осаждения 900оС.
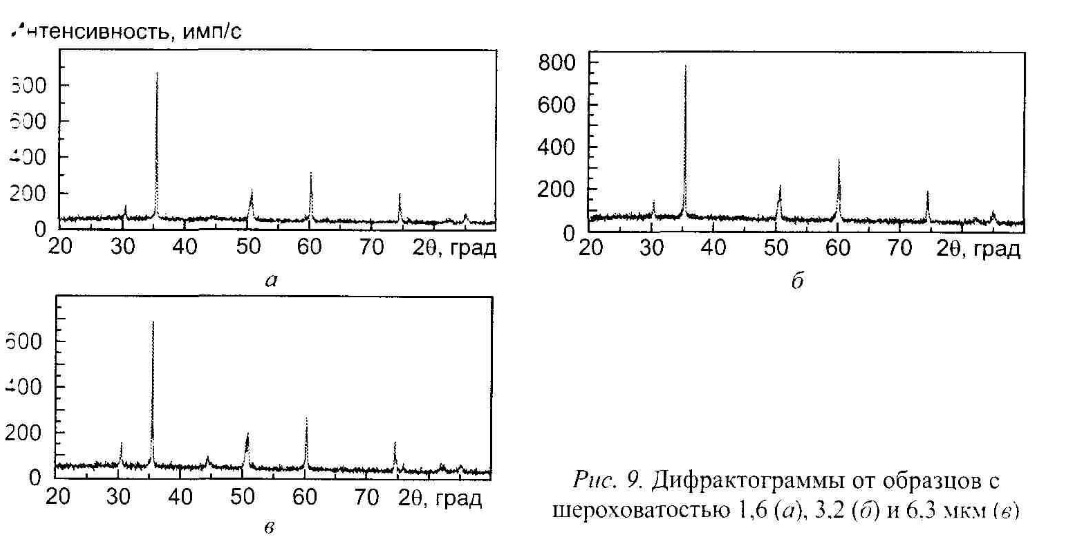
Выводы
Подтверждена возможность получения двухслойных защитных покрытий металл—керамика электронно-лучевым способом за один технологический цикл. Установлено существенное влияние контролируемых технологических параметров осаждения на структуру внешнего керамического слоя. Подтверждена возможность регулирования высокоплотной зоны в керамическом слое путем изменения температуры и скорости осаждения. Показано, что фазовый состав внешнего керамического слоя можно регулировать путем изменения температуры и скорости осаждения. С увеличением указанных параметров количество тетрагональной фазы в данном слое возрастает. Фазовый состав внешнего керамического слоя практически не зависит от шероховатости поверхности, на которую осуществляется осаждение, и толщины слоя.
1. Мовчан Б. А., Малашенко И. С. Жаростойкие покрытия, осаждаемые в вакууме. — К.: Наук, думка, 1983. — 230 с.
2. Гречанюк Н. ИКучеренко П. П., Осокин В. А., Шпак П. А. Современное состояние и перспективы создания теплозащитных покрытий (ТЗП) для лопаток газотурбинных установок (ГТУ) и оборудования для их нанесения // Новини енергетики. — 2000 — Я§ 9. —С. 32—37.
3. Мовчан Б. А., Малашенко И. С., Яковчук К. Ю. Двух- и трехслойные покрытия, получаемые осаждением в вакууме, для защитных покрытий лопаток газовых турбин // Автомат. сварка. — 1994. —№2. — С. 30—38.
4. Жадкевич А. Л., Савченко В. И., Слюняев С. В. и др. Очистка лопаток ГТУ от эксплуатационных загрязнений АГД потоками // Тяжелое машиностроение. — 1993. — № 2. — С. 34—36.
5. Жерздев С. В., Тамарин Ю. А., Лопатин Е. В. Исследование влияния содержания иттрия на фазовый состав спеченных и конденсированных керамик системы ZrOj—-Y2O3 И Пробл. спецэлектрометаллургии. — 1991. — № 11. — С. 53—55.
6. Мартиросян А. А., Градин В. В, Гречанюк И. И. и др. Влияние скорости конденсации на структуру покрытий из стабилизированного диоксида циркония // Там же. — 1987. — № 2. — С. 47—51.
7. Малашенко И. С., Марайниссен Г. X, Белоцерковский В. А. и др. Долговечность конденсационных покрытий NiCoCrAlY—ZrC>2—8 У20з при термоциклическом нагружения // Там же. — 1997. — № I. — С. 34—46.
8. Sheffler К., Gupta D. Current status and future trends in turbine application of thermal barrier coatings If Trans. ASME. J. Eng. Gas Turbines and Power. — 1988. — 110, No. 7. — P. 605—609.